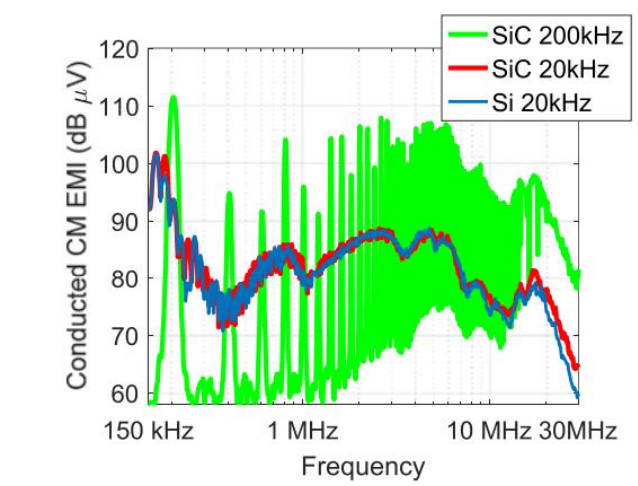
Wide-bandgap materials are revolutionizing power devices, enhancing performance and efficiency. Traditional silicon faces limitations as power demands rise. Silicon carbide and gallium nitride, key WBG materials, offer high switching frequency, low losses, and high-temperature operation, making them ideal for power devices.
These materials result in reduced energy losses and increased power density, especially beneficial in electric vehicle converters and renewable energy inverters. WBG’s unique electrical properties enable compact, lightweight, and efficient power electronics, contributing to a greener energy landscape.
WBG materials also impact aerospace and telecommunications, offering high-frequency capabilities for efficient satellite systems and communication devices. As demands for miniaturization and performance intensify, WBG materials drive technological advancements, ushering in an era of energy-efficient and high-speed electronic solutions.
Ongoing research and development in WBG materials promise continued integration into power devices, reshaping the possibilities and efficiencies across diverse sectors.
Exploring the Dominance and Functionality of WBG Devices in Motor Drives
Motor drives, the fundamental element of electromechanical systems, serve as the vital link connecting machinery and devices seamlessly. These drives govern the speed, torque, and direction of electric motors, transforming electrical energy into precise mechanical motion. Thus, achieving maximum efficiency and precision in motor drives is paramount. Consequently, Wide Bandgap (WBG) devices are finding integration into motor drives across various applications, including high-speed motors, low-inductance motors, and electric drives operating in elevated temperatures.
For instance, low-inductance motors can benefit from Si MOSFETs, capable of switching up to 50 kHz and providing the desired current ripple, enhancing reliability and efficiency. In contrast, traditional materials like Si lack the necessary critical electric field, as illustrated in Figure 1, making WBG devices the preferred choice for electric drives.
Compare electrical parameters in Wide bandgap materials and Silicon
Conversely, the surge in high-speed electric machines’ popularity stems from their heightened power density, achieved by seamlessly integrating the motor with a compressor through a gearbox. Recognizing the high-frequency capability of SiC Mosfets played a pivotal role, enabling the motor to synchronize with the compressor, obviating the need for a gearbox. This singular innovation alone augmented the reliability and efficiency of GaN-based systems by approximately 4 percent compared to traditional Si-based motor drives.
Semiconductors with broader bandgaps exhibit superior performance at elevated temperatures compared to conventional silicon. The adoption of integrated motor drives has soared as they replace less efficient online direct motors. However, the proximity of the converter and motor elevates temperatures significantly. Hence, the development of Wide Bandgap (WBG) power modules, boasting high frequency and reverse voltage blocking, proves to be an optimal solution for high-temperature applications like Integrated Motor Drives (IMD).
Surmounting Challenges to Unleash the Full Potential of Wide Bandgap Devices in Motor Drive Systems
Wide bandgap devices offer advantages for high-temperature, high-speed, and low-inductance motors. Nevertheless, these devices produce substantial Electromagnetic Interference (EMI), escalating with higher switching frequencies. Figure 2 illustrates a comparison of conducted EMI performance among various wide bandgap devices. It is evident that during switching transients, SiC JFET inverter exhibits elevated parasitic oscillations, serving as the primary source of noise and reduced efficiency.
Comparing Common Mode EMI of SiC MOSFET and Si IGBT-based Motor Drives
Addressing this concern, various inventive CM voltage cancellation and filter topologies are implemented for Wide Bandgap (WBG) devices, markedly minimizing EMI generation. Additionally, an integration of dual winding stator configuration and inverter topology is employed, as depicted in Figure 3. Specifically designed for PWM motor drives with symmetrical circuits, this approach nullifies the complementary CM voltage, thereby reducing overall EMI in the system.
Innovative CM Voltage Cancellation Inverter Topology with Dual Winding Stator
In Summary
Wide Bandgap (WBG) devices play a pivotal role as essential facilitators across diverse motor drive applications, demonstrating notable advantages in low-inductance motors, high-speed motors, and high-temperature environments. The incorporation of WBG devices in electric drive applications yields substantial improvements in power density, dynamic response, and overall energy efficiency. However, unlocking the full potential of WBG devices necessitates intricate converter design.
Specifically, well-designed gate drivers are imperative, ensuring swift switching with minimal overshoot and losses. The converter design must also address challenges like minimizing parasitic inductance in the commutation loop and implementing rapid short-circuit protection for WBG switches. These considerations are paramount for optimizing performance and realizing the complete benefits of WBG devices in motor drive systems.
To justify the higher cost of Wide Bandgap devices and fully leverage their capabilities, rapid switching is essential. However, this increased speed leads to higher Electromagnetic Interference (EMI) production. The rapid voltage change in the motor induces a type of current known as Common Mode, potentially harming the motor’s insulation. Opting for slower switching of WBG devices aligns with current insulation standards for motors, allowing the use of EMI control methods akin to those in drives based on Insulated Gate Bipolar Transistors (IGBTs). However, the trade-off is that slower speeds compromise the full utilization of the power and efficiency advantages offered by WBG devices, crucial for balancing their higher cost.
In response to these challenges, emerging technologies like the integration of inverter topology and dual winding stator configurations are introduced. These innovations aim to mitigate EMI generation at higher speeds and voltages, striking a balance between efficiency and cost-effectiveness in WBG-based motor drive systems.