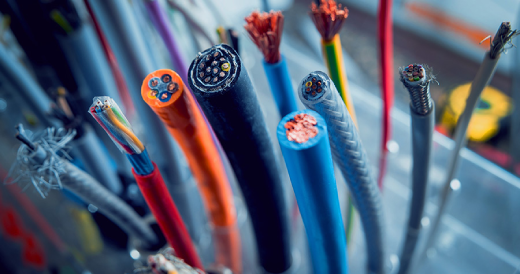
Do You Know About Power Cables?
What is Power Cables?
An electrical system’s wires are a crucial part. Transferring electrical energy from one place to another is its job. These cables are available in numerous varieties and setups. Every cable is made to adhere to particular voltage specifications. Present capabilities and surroundings Usually, electrically conductive materials like copper or aluminum are used to make the wires. For longevity and safety, they are insulated and frequently covered with a protective coating.
How Power Cables Work
Investigating the fundamentals of electrical transmission is necessary to comprehend how wires function. the function of shielding and insulation as well as the intricate procedures involved in the distribution and transmission of electricity.
Basics of Electrical Conductivity
The ability of a material to permit electric current to flow through it is the primary definition of conductivity. Materials like copper or aluminum that conduct electricity are used in cables. Its superior electrical conductivity makes it useful. The free electrons within these materials move in reaction to the application of an electric potential. generating a current of electricity The movement of electrons powers our systems and gadgets. A wire’s ability to carry electricity depends on a number of variables, including the material’s purity. both temperature and cross-sectional area.
Role of Insulation and Shielding
As a barrier between the conductive core and the outside world, insulators are crucial components of electrical wires. In the absence of insulation, electrical leaks may happen. Power outages and safety risks result from this. PVC (polyvinyl chloride) and XLPE (cross-linked polyethylene) are two common insulation materials that are used because of their great insulating qualities and robustness. Additionally, they are insulated to shield cables from radio frequency and electromagnetic interference (EMI). interference (RFI) Utilize shielding materials to maintain continuous transmission, such copper foil or aluminum foil. stacked all the way around the edge. Insulation reduces outside interference and maintains the electric field inside the cable.
Transmission and Distribution of Electricity
Power lines are used to transmit and distribute electricity across long distances through a complicated network of equipment. The energy used in the plant is produced either from shared or renewable resources. The voltage will be raised in order to facilitate effective long-distance signal transmission. This electricity is sent to substations via high-voltage transmission lines. After that, it is reduced to low voltage and distributed to residences, companies, and industries. Low impedance cabling is required throughout this route to minimize power losses and guarantee dependable distribution. Superconducting cables and smart grids are examples of cutting-edge technologies that are always developing to increase the power transmission and distribution grid’s dependability and efficiency.
Applications of Power Cables
Residential Uses
There are electrical cables all throughout the place where people live. They make it easier for power to be distributed throughout the house for illumination. Using home equipment for heating, cooling, and lighting from cables buried in walls to overhead wires tying neighborhoods together. Power cables guarantee a dependable and secure power source. To provide for the residents’ everyday necessities Modern cable technology contributes to both increased safety and energy savings in the home by offering features like energy-efficient conductors and fireproof insulation.
Commercial and Industrial Uses
Within the commercial and industrial domain, cabling serves as the central nervous system for machinery, equipment, and auxiliary infrastructure that are essential to corporate operations. Cabling enables power to be supplied to lights, HVAC, and manufacturing operations in factories and office buildings. and data center effectively Heavy loads, extreme temperatures, and severe conditions are all things that industrial grade cables are made to resist. This guarantees that vital processes never lose power.
Renewable Energy Projects
Wind farms and other renewable energy installations require a lot of electricity lines. Hydroelectric power plants and solar power plants Link to the grid and supply customers with electricity. The produced energy is moved from remote locations to populated regions via high-voltage wires. removing geographical constraints and making the most use of renewable resources possible. Modern electrical infrastructure can integrate clean energy by using creative cable designs, including underwater cables for offshore wind farms. Minimize your reliance on fossil fuels and your influence on the environment.
Special Applications (e.g., Undersea, Aerospace)
Specialized uses for wires can be found in aircraft and subsea environments. Robust and dependable solutions are necessary for harsh circumstances and distinct problems. Massive water pressure is something that underwater cables are meant to handle. This makes it possible to connect offshore facilities and transfer power across continents. within the aerospace industry To power aviation equipment, lightweight, temperature-resistant cables are needed. satellites for communication and space exploration projects Every part needs to fulfill strict requirements for both performance and safety. These specialized cables are crucial to the advancement of global connection, scientific research, and exploration.
Installation Process and Best Practices
Careful planning, preparation, and execution are necessary for the cabling installation procedure in order to maximize aspects such cable type and minimize risk. Route choice During installation, correct termination procedures and trench or overhead installation should be taken into consideration. Observing the manufacturer’s instructions is one of the best practices. adherence to regional building laws and ordinances. Make sure there is enough clearance and support to avoid sagging or mechanical stress, as well as appropriate cable management to prevent damage. The dependability and integrity of the electrical system will be improved by hiring a qualified and experienced electrician or contractor to install the cables.
Routine Maintenance and Troubleshooting
In order to detect and address possible issues before they become an expensive outage or safety risk, routine maintenance is essential. Wear, corrosion, and insulation degradation can be identified with the aid of routine testing, inspections, and preventative maintenance measures. or being too hot Finding and fixing issues like short circuits, insulation failures, or cable damage is known as troubleshooting. the use of methodical examination and evaluation. Intervention in emergency maintenance, including swapping out or mending broken cables. Connector cleaning or connection tightening By doing this, the power source is protected from malfunctions. and lower the possibility of accidents or power outages.
Identifying Common Problems
Electrical wires frequently experience corrosion, mechanical damage, insulation failure, and overheating. as well as conductor exhaustion Excessive current might lead to overheating. inadequate airflow or an inadequate cable size Insulation deterioration and a fire threat follow from this. Age may be the cause of insulation breakdown. environmental variables or flaws in the manufacturing process Conductors become visible as a result, and the cable’s dielectric qualities are diminished. The integrity of the cable is compromised and resistance is increased by corrosion brought on by exposure to chemicals or moisture. Insulation or conductors may break due to mechanical damage from bending, collision, or friction. Conductor fatigue brought on by frequent vibration or bending. This could result in electrical problems and hasten the material’s wear and tear.
Preventive Measures
The secret to lowering frequent wiring issues and prolonging the lifespan of the electrical system is to take preventive action. Inspection guidelines Upkeep Testing frequently aids in spotting possible issues early on and solving them before they get worse. Using suitable cable installation techniques, such as routing, bracing, and sufficient protection minimizes tension on the cable and guards against mechanical damage. Sensors for measuring temperature and humidity in the environment warn operators of potential problems that could compromise the functionality of the cable. Making the switch to sturdy, high-quality wires with better insulation and shielding can increase dependability and lessen vulnerability to external influences. A proactive attitude to cable maintenance is encouraged and industry standards are ensured when management staff is trained in maintenance and appropriate safety practices.