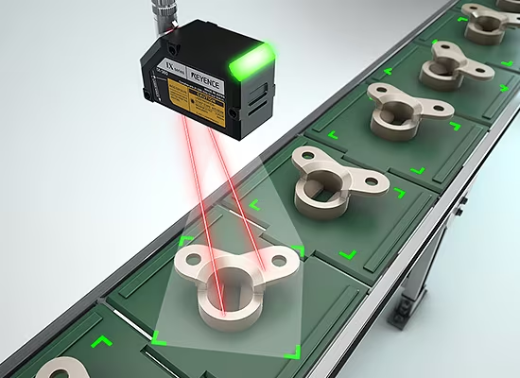
Laser Position Sensors
What is Laser Position Sensors?
Laser position sensors are devices designed to precisely measure the position and movement of objects in various applications. They operate on the triangulation concept, which uses measurements of the angle and length of the reflected laser beam to pinpoint an object’s location. Even at great distances, this approach enables very accurate readings. Laser position sensors are a useful tool in industries where accurate positioning is critical because they can calculate a target’s position with extraordinary accuracy by analyzing the properties of reflected light.
How Laser Position Sensors Work
A laser beam is emitted by laser position sensors toward the target. After reflecting from the target’s face, the laser beamre-enters the sensor. The sensor determines the precise position of the target with respect to its position by measuring the angle of the reflected beam and the distance between the target and the sensor. Because it uses triangular figure to calculate the position, this procedure is constantly appertained to as triangulation. Laser position sensors enable precise positioning in a range of applications by measuring useable angles and distances with high accuracy using sophisticated optics and electronics.
Main Components of Laser Position Sensors
1. Laser Source
The coherent light beam directed at the target is produced by the laser source. The laser must remain stable and harmonious in order to give precise measures. colorful kinds of lasers, including semiconductor or diode lasers, might be employed grounded on the particular requirements of the operation.
2. Receiver
The receiver detects the reflected laser beam and captures relevant data, such as intensity and angle. It converts this optical signal into an electrical signal that can be processed further. Receivers in laser position sensors are often equipped with photodiodes or photodetectors capable of detecting even weak signals accurately.
3. Signal Processing Unit
The signal processing unit is in charge of determining the target’s precise position by assaying the data it has entered from the receiver. Taking into consideration rudiments including the angle of reflection, the distance traveled, and any environmental circumstances that can alter the results, it uses algorithms to interpret the data gathered from the reflected laser beam. Laser position sensors can achieve excellent precision and reliability in a variety of operating circumstances thanks to advanced signal processing techniques.
Applications of Advanced Laser Position Sensors
Advanced laser position sensors are largely protean and have several operations across multiple diligence because of their delicacy, perfection, andnon-contact nature. Then are a many noteworthy uses:
1. Manufacturing and Industrial Automation
Quality Control: To make sure particulars match specifications, laser sensors are employed to measure products’ confines, consistence, and face biographies.
Robotics: They make it possible for robotic arms to be precisely deposited and guided, adding assembly line robotization.
Machine Tool Alignment: To insure high- perfection affair, laser examinations are used to align and calibrate CNC machines.
2. Aerospace and Defense
Aircraft Assembly: Guarantees that each component is precisely aligned and fitted during assembly.
Navigation Systems: Used in inertial navigation systems to provide accurate positional data.
Targeting and Range Finding: Necessary to guarantee aiming accuracy for military range equipment and missile guidance.
3. Automotive Industry
Assembly Line Automation: Used to align and position auto parts during assembly.
Vehicle Dynamics Testing: Needles effects like wheel alignment, suspense trip, and distortion of the lattice while the vehicle is loaded.
Autonomous Vehicles: Equipped with LIDAR systems, which collude the surroundings to prop in handicap avoidance and navigation.
4. Medical and Healthcare
Surgical Navigation: This helps ensure precise instrument positioning, particularly in minimally invasive surgery.
Patient Positioning: Guarantees that patients receiving radiation therapy and diagnostic imaging are positioned accurately.
Biomedical Research: Motion and biological tissue stresses are studied in biomechanics.
5. Construction and Civil Engineering
Structural Monitoring: Quantifies the displaced and deformed parts of bridges, buildings, and other structures.
Alignment of Machinery: Guarantees precise alignment and installation of heavy construction equipment.
Topographic Mapping: Utilized in surveying to create accurate topographic maps and models of construction sites.
6. Electronics and Semiconductor Industry
Wafer Inspection: Used to hand semiconductor wafer consistence, flatness, and other characteristics.
Component Placement: Guarantees that electronic factors are deposited precisely on published circuit boards.
MEMS Device Testing: Essential for microelectromechanical system (MEMS) testing and alignment.
7. Telecommunications
Fiber Optic Alignment: Guarantees precise optical fiber alignment for the least amount of signal loss.
Antenna Positioning: Utilized to place antennas precisely for the best possible transmission and reception of signals.
8. Research and Development
Scientific Experiments: Provides high precision measurement capabilities essential for various scientific experiments.
Material Testing: evaluates the characteristics of a material under various circumstances, including deformation, stress, and strain.
Environmental Monitoring: utilized to track occurrences and changes in the environment through remote sensing.
9. Consumer Electronics
3D Scanning and Printing: Integral in 3D scanners for capturing precise details of objects to be printed.
VR/AR Systems: Used in tracking movements and positioning in virtual and augmented reality systems.
Gaming: Enhances interactive gaming experiences through precise motion tracking.
10. Energy and Utilities
Wind Turbine Monitoring: To guarantee effective operation, detects vibration and distortion of the blades.
Solar Panel Alignment: Makes sure the panels are deposited as optimally as possible to absorb the most energy possible.
Pipeline Monitoring: This fashion finds pipe deportations and distortions to stop leaks and other problems.
These uses demonstrate the adaptability and vital role that cutting-edge laser position sensors play in raising precision, effectiveness, and safety across a range of sectors.
Conclusion
In conclusion, cutting- edge laser position sensors give unmatched perfection, delicacy, and rigidity across a broad diapason of uses and sectors. In diligence ranging from robotics and manufacturing to aerospace, healthcare, and automotive, these sensors are essential for boosting affair, effectiveness, and product quality. Laser sensors grease bettered control and robotization, leading to advanced productivity and lower time-out, by giving real- time data on position and stir. To fully realize the benefits of laser sensor technology, despite its many advantages, issues including cost, technological limitations, and environmental variables must be properly taken into account.