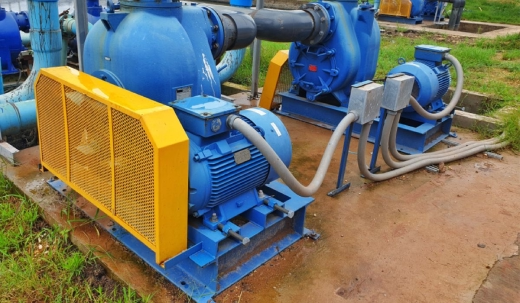
Pumps
What are Pumps?
Pumps are essential pieces of machinery in artificial installations. It serves a pivotal purpose in moving liquids from one position to another. Its capacity to move liquids or gasses effectively is what makes it significant. Assist in the several procedures needed for infrastructure development, energy production, and manufacturing.
Types of Industrial Pumps
Centrifugal Pumps
The centrifugal force proposition underlies the operation of centrifugal pumps. where the pump covering’s impeller spins As a result, the liquid is forced out from the center of gyration by a centrifugal force. The liquid gains kinetic energy from its movement. As it exits the pump vent, this is transformed into pressure. For applications needing high flow rates and moderate pressure, centrifugal pumps are quite effective. Because of this, they are essential in sectors like water treatment, where they are used to pump treated, raw, and wastewater throughout the treatment process. Additionally, it is necessary for the transmission of bases, acids, and liquids. transfer of caustic liquids with less damage to internal parts.
Positive Displacement Pumps
A set volume of fluid is captured and exchanged by positive displacement pumps at each cycle. It is powered by a rotary or piston mechanism. When a piston pump pushes fluid through the pump using a diaphragm or plunger. In contrast, rotary pumps employ revolving gears, lobes, or impellers to facilitate the movement of liquid within the pump chamber. Applications requiring accurate flow control and the capacity to handle viscous, thick, or shear-sensitive materials (such as those in the oil and gas sector) are well suited for these pumps. Chemicals are pumped and injected using positive pumps. including the shipping of refined goods and crude oil. Likewise in food processing they are crucial for pumping components such as syrups, sauces and batters to preserve product integrity and consistency throughout the production process.
Operating Principles
Fluid Dynamics
Fluid dynamics within pumping systems involve the interplay of pressure and flow dynamics crucial for efficient operation. The way the pump produces the force needed to move the fluid against resistance is determined by pressure dynamics. This guarantees that the system’s flow rates are sufficient, and flow dynamics regulates the flow and distribution of fluids through pipelines and operations. This affects turbulent and laminar flow, among other things. and the pressure decreases The viscosity and temperature of the fluid are two examples of factors that greatly affect pump performance. Viscous fluids require pumps with enhanced power to overcome resistance, while temperature fluctuations can affect fluid properties, altering viscosity and flow characteristics.
Pump Components
Impellers, casings, and seals are the essential parts of industrial pumps, and each is crucial to preserving the dependability and efficiency of the pump. By employing centrifugal force to accelerate a fluid outward, the impeller is a revolving part that gives fluid energy. The frame that encircles the impeller establishes the necessary pressure differential for pumping and controls the direction of fluid flow. Seals keep the pressure integrity inside the pump and stop leakage. This is particularly crucial when working with fluids that are toxic or caustic.
Industrial Applications
Water and Wastewater Management
Pumps are essential factors of external water systems because they make it easier for water to move from the source to the treatment installation and the distribution system. Pumps are used in water treatment installations to raise water out of wells or budgets. This guarantees a steady flow of water for activities like disinfection and filtration. Through a system of pipes and storage facilities, they also assist in the distribution of treated water to consumers who are residential, commercial, and industrial. Pumps are essential to wastewater management because they move sewage and wastewater from industrial plants to treatment facilities. Prior to being recycled or disposed of securely, they undergo purification. In these operations, the sustainability of the environment and public health depend heavily on the efficiency and dependability of the pumps. To ensure security and avoid downtime. These parts need to be inspected and maintained on a regular basis. Searching for signs of wear and tear is one part of examination. to increase effectiveness and prolong the pump’s lifespan. Seals should be kept properly greased and replaced as needed.
Chemical and Petrochemical Industries
In the chemical and petrochemical industries, pumps are pivotal to the movement of sharp liquids. For these companies, pumps are pivotal to the movement of chemicals between storehouse tanks. Reactors and processors used safely and effectively. This is a result of how potent these drinks are. Certain materials and designs are needed for survival. This ensures a long service life and guards against leaks or contamination that would endanger public health. When choosing and using a pump, safety is crucial. Among the many factors are a carefully designed leakage prevention system, mechanical integrity, and material compatibility. In corrosive chemical conditions, using the appropriate materials—such as stainless steel or corrosion-resistant alloys—increases pump life and reliability. In petrochemical and chemical applications, pumps are crucial to preserving overall operating effectiveness. We also place a high priority on safety and environmental preservation.
Efficiency and Sustainability
Energy Efficiency
Efficiency in industrial pump systems is becoming more and more crucial. Variable speed drives (VSD) are one technology that makes it possible for the pump to change its speed in response to demand. through balancing output with real demand. Rather than operating at maximum efficiency all the time, this optimization will drastically cut down on energy usage. This is a result of the pump’s increased ability to handle various loads with efficiency. The benefits to the environment go beyond financial reductions. By reducing energy consumption during peak hours and carbon emissions, the use of VSD not only improves operational flexibility. However, it also enhances overall system efficiency and minimizes resource use, which supports sustainable practices.
Maintenance Strategies
Optimizing pump life and reliability requires a well-thought-out maintenance plan. Advanced monitoring technologies and data analysis are used in predictive maintenance procedures to identify any issues before they result in downtime. Maintenance teams can identify early symptoms of wear or failure and plan proactive intervention times by analyzing pump performance indicators such as vibration, temperature, and fluid characteristics. Timely repairs and routine inspections are equally crucial. This guarantees that parts like impellers, bearings, and seals continue to operate at their best. In addition to lowering the possibility of unplanned malfunctions, proactive maintenance increases operational safety and continuity. Increase equipment longevity and reduce resource usage to support sustainable operations.