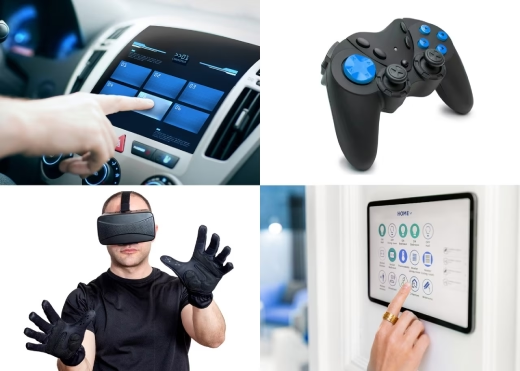
Piezoelectric-Actuators
Piezoelectric actuator transducers are devices that use the piezoelectric effect to convert electrical energy into mechanical motion.
Working Principle
– Piezoelectric Effect: A piezoelectric substance undergoes a modest form change when exposed to an electric field. Examples of such materials are quartz and some ceramics. This deformation can be used to create precise mechanical movements.
– Operation: A piezoelectric material expands or contracts in response to voltage applied to it. This motion can be used to drive mechanical components.
Advantages
– High Precision: Capable of very fine movements and adjustments.
– Fast Response Time: Quick to react to electrical signals.
– Small Size: Incredibly small, which qualifies it for tiny applications.
Disadvantages
– Limited Displacement: Generally speaking, micrometer-sized displacements are the only ones that piezoelectric actuators are capable of producing.
– High Voltage Requirements: It frequently takes high voltages to produce noticeable displacement.
– Non-linear Behavior: Their response can be non-linear and may vary with temperature and applied voltage.
Enhancing Precision in Robotics
1. High-Resolution Positioning
Mechanisms for Achieving Fine Positional Control:
– Closed-Loop Control Systems: Utilizing feedback mechanisms to continuously monitor and adjust the position of the robotic arm or tool. Common sensors include encoders and resolvers.
– Precision Gear Systems: Good motion control is offered by precision gears or high gear ratio gears, such as those found in harmonic drives.
– Linear Stages and Actuators: Provide for exact linear motion and positioning, such as the nanoscale positioning stages seen in microscopes.
– Piezoelectric Actuators: When an electric field is applied, they can stretch or compress to produce extremely tiny motion.
Examples of Applications Requiring High-Resolution Movements:
– Micro-manufacturing: Jobs like inserting tiny electronic parts into circuit boards.
– Medical Robotics: For surgical robots to carry out delicate operations, extreme precision is needed.
– Optics and Microscopy: Modifying mirrors and lenses in image systems with high resolution.
2. Rapid and Accurate Movements
How Piezoelectric Actuators Contribute to Fast Response and Precise Adjustments:
– Fast Response Times: Piezoelectric actuators can move in microseconds, allowing for rapid adjustments.
– High Precision: Sub-micrometer precision because of the capacity to produce small movements.
– Low Hysteresis and High Stiffness: Permits more precise and reliable placement.
Case Studies or Examples of Rapid Movement Applications in Robotics:
– Scanning Probe Microscopes (SPMs): Makes use of piezoelectric actuators to quickly and accurately scan surfaces.
– Optical Fiber Alignment: Piezoelectric actuators in the telecommunications industry precisely position optical fibers to guarantee effective transmission.
– Fast Camera Autofocus: Piezoelectric actuators are used by certain high-speed cameras to rapidly and precisely change the lens position.
3. Stable and Reliable Performance
Piezoelectric actuators’ effects on robotic systems’ stability and dependability:
– Reduced Vibration: Because piezoelectric actuators often have smaller moving masses and moments of inertia, they increase system stability and lessen vibration.
– High Repeatability: High degree of reproducibility This is crucial for reliable performance on repeated tasks since it allows for exact control.
– Robust Performance: Piezoelectric actuators are perfect for demanding applications since they are typically long-lasting and dependable.
Examples of Systems or Robots Benefiting from This Stability:
– Automated Assembly Lines: Robots used in manufacturing benefit from stable and reliable performance for consistent and high-quality production.
– Aerospace Applications: Precision and stability are crucial for robotics used in spacecraft or satellite assembly.
– Laboratory Automation: Systems in scientific labs, where stable and accurate operations are essential for experiments and analysis.
Applications in Robotics
Manufacturing and Automation
Role in Precise Assembly and Handling Tasks:
– Accurate Positioning: In the automated assembly For jobs like aligning or positioning tiny electronic components, piezoelectric actuators’ exceptional precision in handling fragile components is crucial.
– Fast and Reliable Operation: Allows for quick movement and adjustment, enhances overall performance, and shortens production cycle times.
Examples of Applications in Automated Production Lines:
– Electronics Manufacturing: Accurate placement of tiny parts on printed circuit boards (PCBs).
– Packaging: Accurate handling and placement of the item throughout the packing procedure.
– Quality Control: Precise modifications to the inspection system to guarantee consistency and quality of the output.
Aerospace and Defense
Precision Requirements in Aerospace Applications:
– Structural Adjustments: Precision changes, such as antenna placement in satellite and spacecraft components or mirror placement in telescopes, are made in the aerospace industry using piezoelectric actuators.
– Flight Control Systems: Helps to precisely regulate the flying system, which comprises the aircraft’s control surfaces and stability.
How Piezoelectric Actuators Meet These Needs:
– High Precision: The capacity to make small, precise movements is necessary for aerospace applications where there are high precision requirements.
– Lightweight and Compact: In aerospace applications where weight and space are critical, small dimensions and low weight are advantageous.
– Reliability and Durability: Because of its resilience, the piezoelectric actuator can resist the challenging circumstances seen in aerospace and space environments.
Expanding Applications
Prospective domains and potential uses of piezoelectric actuators in robotics:
– Biotechnology: Creation of highly accurate robotic systems for DNA sequencing and cell manipulation.
– Agriculture: Utilized in high-precision crop health monitoring and seed sowing automation in precision agriculture.
– Consumer Electronics: Integration with gadgets like tablets and smartphones to provide haptic feedback systems or touch interfaces.
– Environmental Monitoring: Robotic systems applications for data collecting and environmental sensing in difficult or dangerous areas.