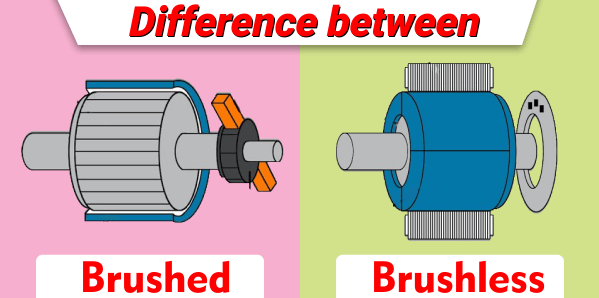
Brushless motor: A brushless DC motor consists of a motor body and a driver. It is a typical electromechanical integration product. Since the brushless DC motor operates in a self-controlled manner, it does not have an additional starting winding on the rotor like a synchronous motor that starts under heavy load under variable frequency speed regulation, and it will not produce oscillation and loss of synchronization when the load changes suddenly. The permanent magnets of small and medium-capacity brushless DC motors now mostly use high magnetic energy level rare earth neodymium iron boron (Nd-Fe-B) materials. Therefore, the volume of the rare earth permanent magnet brushless motor is smaller than that of the three-phase asynchronous motor of the same capacity.
Brushed motor: A brushed motor is a rotating electrical machine that contains a brush device to convert electrical energy into mechanical energy (motor) or mechanical energy into electrical energy (generator). The difference from brushless motors is that the brush device is used to plug in or out. The brush motor is the basis of all motors. It has the characteristics of fast starting, timely braking, smooth speed regulation in a wide range, and relatively simple control circuit. Features.
Ⅰ.The difference between the working principles of brushless motors and brushed motors
How brush motors work
Brushed motors are the first type of motor that everyone comes into contact with. In middle school, the introduction of motors in physics classes was also based on them as a model. The main structure of a brush motor is stator + rotor + brush, which obtains rotational torque through a rotating magnetic field to output kinetic energy. The brushes and the commutator are in constant contact and friction, and play a role in conduction and phase commutation during rotation.
Brushed motors use mechanical commutation, so the magnetic poles don’t move and the coils rotate. When the motor is working, the coil and commutator rotate, but the magnets and carbon brushes do not rotate. The alternating changes in the direction of the coil current are completed by the phase commutator and brushes that rotate with the motor.
In brush motors, this process is to arrange the two power input terminals of each group of coils into a ring in sequence, separated by insulating materials, forming a cylinder-like thing that is integrated with the motor shaft. Through two small pillars (carbon brushes) made of carbon elements, under the action of spring pressure, two points on the upper coil power input ring cylinder are pressed from two specific fixed positions to energize a set of coils.
As the motor rotates, different coils or different poles of the same coil are energized at different times, so that the N-S poles of the magnetic field generated by the coils have a suitable angle difference with the N-S poles of the nearest permanent magnet stator. Opposite poles of the magnetic fields attract each other, and the same poles of the same coil are attracted. Repulse each other, generate force, and push the motor to rotate. The carbon electrode slides on the coil terminal, like a brush brushing on the surface of an object, so it is called a carbon “brush”.
If they slide against each other, the carbon brushes will rub against each other, causing wear and tear. The carbon brushes need to be replaced regularly. The on-off alternation between the carbon brushes and the coil terminals will cause sparks and electromagnetic damage, which will interfere with electronic equipment.
How does a brushless motor work?
In brushless motors, the commutation work is completed by the control circuit in the controller (usually a Hall sensor + controller, and the more advanced technology is a magnetic encoder).
Brushless motors use electronic commutation, the coil does not move and the magnetic pole rotates. Brushless motors use a set of electronic equipment to sense the position of the permanent magnet poles through Hall elements. Based on this perception, electronic circuits are used to timely switch the direction of the current in the coil to ensure that the magnetic force in the correct direction is generated to drive the motor. . Eliminates the disadvantages of brushed motors.
These circuits are motor controllers. The controller of a brushless motor can also implement some functions that a brushed motor cannot, such as adjusting the power switching angle, braking the motor to reverse rotation, locking the motor, and using the brake signal to stop powering the motor. Nowadays, the electronic alarm lock of battery vehicles makes full use of these functions.
The brushless DC motor is composed of a motor body and a driver and is a typical electromechanical integration product. Since the brushless DC motor operates in a self-controlled manner, it does not have an additional starting winding on the rotor like a synchronous motor that starts under heavy load under variable frequency speed regulation, and it will not produce oscillation or loss of synchronization when the load changes suddenly.
Ⅱ.Brushless motor vs. Brush
Brushed motors have simple structure, long development time and mature technology.As early as the birth of the motor in the 19th century, the most practical motor produced was the brushless form, that is, the AC squirrel cage asynchronous motor. This kind of motor has been widely used after the generation of alternating current. However, asynchronous motors have many insurmountable defects, resulting in slow development of motor technology. In particular, brushless DC motors have never been able to be put into commercial operation. With the rapid changes in electronic technology, they have only been slowly put into commercial operation in recent years. In essence, they still belong to the category of AC motors.
Not long after the brushless motor was born, people invented the DC brush motor. Because the DC brush motor has a simple structure, is easy to produce and process, is easy to maintain, and is easy to control; the DC motor also has fast response, large starting torque, and the ability to provide rated torque from zero speed to rated speed, so once it came out It has been widely used.
DC brush motor has fast response speed and large starting torque
The brushed DC motor has fast starting response, large starting torque, smooth speed change, and almost no vibration from zero to maximum speed, and can drive a larger load when starting. The brushless motor has a large starting resistance (inductive reactance), so the power factor is small, the starting torque is relatively small, there is a buzzing sound when starting, accompanied by strong vibration, and the load is small when starting.
The brushed DC motor runs smoothly and has good starting and braking effects
The brushed motor regulates speed through voltage regulation, so it starts and brakes smoothly, and runs at a constant speed smoothly. Brushless motors are usually controlled by digital frequency conversion, which first converts AC into DC, then DC into AC, and controls the speed through frequency changes. Therefore, brushless motors run unstable and vibrate greatly when starting and braking. Only when the speed is constant will be stable.
DC brush motor has high control accuracy
DC brush motors are usually used together with reduction gearboxes and decoders, which make the motor have greater output power and higher control accuracy. The control accuracy can reach 0.01 mm, which allows the moving parts to stop almost anywhere you want. All precision machine tools use DC motors to control accuracy. Because the brushless motor is not smooth when starting and braking, the moving parts will stop at a different position every time, and must use positioning pins or limiters to stop at the desired position.
DC brushed motors are low-cost and easy to maintain
Since DC brushed motors have a simple structure, low production costs, many manufacturers, and relatively mature technology, they are widely used in factories, processing machine tools, precision instruments, etc. If the motor fails, you only need to replace the carbon brush, and each Carbon brushes only cost a few yuan and are very cheap. The brushless motor technology is immature, the price is high, and the application range is limited. It should mainly be used in constant-speed equipment, such as variable frequency air conditioners, refrigerators, etc. If the brushless motor is damaged, it can only be replaced.
No brushes, low interference
The brushless motor removes the brush. The most direct change is that there is no spark generated when the brushed motor is running, which greatly reduces the interference of sparks to remote control radio equipment.
Low noise and smooth operation
The brushless motor has no brushes, so the friction during operation is greatly reduced, the operation is smooth, and the noise is much lower. This advantage is a huge support for the stability of the model’s operation.
Long life and low maintenance cost
Without the brush, the wear of the brushless motor is mainly on the bearings. From a mechanical point of view, the brushless motor is almost a maintenance-free motor. When necessary, you only need to do some dust removal maintenance.
Ⅲ.Brush motor and brushless motor speed regulation method
In fact, the control of both motors is voltage regulation, but because the brushless DC uses electronic commutation, it can only be realized with digital control, while the brushed DC commutates through carbon brushes, using thyristors, etc. Traditional analog circuits can be controlled and are relatively simple.
1. The brush motor speed adjustment process is to adjust the motor power supply voltage. The adjusted voltage and current are converted by the commutator and brushes to change the strength of the magnetic field generated by the electrodes, thereby achieving the purpose of changing the rotation speed. This process is called variable voltage speed regulation.
2.The brushless motor speed adjustment process is to keep the voltage of the motor’s power supply unchanged, change the control signal of the ESC, and then change the switching rate of the high-power MOS tube through the microprocessor to achieve the change in rotation speed. This process is called variable frequency speed regulation.